Calcário para Cimento
90% da matéria-prima para fabricação do cimento vem deste importante minério
90% da matéria-prima para fabricação do cimento vem deste importante minério
Desde os tempos mais remotos o homem procura um material resistente às condições climáticas e, por isso mesmo, bastante durável. Inicialmente os Egípcios usavam uma espécie de lama encontrada no Rio Nilo e depois um certo tipo de gesso; ambos encontrados até hoje em alguns monumentos e obras. Entretanto, foram os Romanos que apresentaram pela primeira vez um aglomerante que chamaram de caementun, termo que originou a palavra cimento. Séculos depois, em 1824, o construtor inglês Joseph Aspdin patenteou o sistema que perdura até hoje, ou seja, calcário mais argila, finalmente moídos em meio úmido, queimados em forno e depois moídos novamente bem finos. A diferença para os sistemas modernos é a utilização da chamada via seca, ou seja, o material é moído em meio seco.
Atualmente, além do calcário e argilas são utilizados também bauxitas e minérios de ferro, em pequenos volumes, para ajustar as quantidades de óxidos exigidos em todo o processo. Estes óxidos de Cálcio, Sílica, Alumínio e Ferro são responsáveis por 95% da composição química do clínquer. Na maioria dos minerais quartzo, rochas ígneas e sedimentares é abundante a presença de sílica, alumínio e ferro. Porém, o cálcio, que é o principal componente do cimento, apenas é encontrado em alguns tipos específicos de rocha calcária.
Quando se fala em Calcário, pensa-se inicialmente na Cal, que é muito utilizada na construção civil e na correção de solos. De fato, o nome é derivado do termo latino calcarius que significa o que contém cal. Na superfície terrestre os afloramentos de calcário são freqüentes e sob diversas formas, de acordo com a época e tipo de formação. Recebe vários nomes, como mármore, marga ou calcita. Sua composição básica é o Carbonato de Cálcio CaCO3 e, especificamente para a fabricação do cimento, o teor desse carbonato deve ficar entre 80 e 85%.
Porém, como em outros minerais, há também a presença de elementos indesejáveis. No caso do calcário para a fabricação de cimento, o vilão é o óxido de magnésio – MgO – e sua presença é o motivo de muitos cuidados na prospecção e exploração das jazidas. Seu teor é limitado pelas normas nacionais e internacionais. Este óxido, quando entra em contato com a água no concreto ou argamassa, se hidrata, transforma-se lentamente em hidróxido de magnésio Mg(OH)2 e seu volume cresce. Esta expansão pode criar tensões internas suficientes para provocar trincas e fissuras. As normas brasileiras fixam o limite máximo de 6,5% para o teor de óxido de magnésio nos cimentos brasileiros, com exceção para o tipo CP III Cimento Portland de alto-forno, que pela presença da escória não tem limite para o MgO.
O calcário se classifica em três tipos, de acordo com o teor de óxido de magnésio. É chamado de Calcítico se o teor de MgO for menor que 4%. Se o teor ficar entre 4 e 18%, inclusive, será chamado de Dolomítico, e se o teor ficar acima de 18% será chamado de calcário Magnesiano. A estratégia para a pesquisa de jazidas para cimento é obter depósitos minerais com pureza ideal e volume viável para o empreendimento. Contudo, por melhor que seja a jazida, não é encontrado nela apenas um determinado tipo de calcário. O segredo, portanto, é fazer uma mistura dos tipos disponíveis, de tal maneira que não se ultrapasse o limite de óxido de magnésio no cimento produzido com este material.
Na prospecção e desmonte das bancadas de exploração, todo o material é ensaiado e a mina é mapeada de acordo com o tipo de material encontrado. As reservas minerais da Itambé, onde se inclui a Mina Rio Bonito atualmente em exploração -, somam 400 milhões de toneladas. O controle de envio do material para a fábrica é feito com muita atenção pelos técnicos da Mina, com base nos ensaios realizados pelo laboratório, que coleta amostras a cada duas horas. A média dos resultados é então utilizada para a remessa do calcário que irá compor a chamada pilha de pré-homogeneização. Desta maneira, fica garantido o atendimento às normas brasileiras neste importante item de controle, já que a segurança das obras deve sempre ser o principal cuidado.
Créditos: Engº Jorge Aoki – Gerente de Assessoria Técnica Itambé
Jornalista Responsável: Rosemeri Ribeiro Mtb. 2696
Cadastre-se no Massa Cinzenta e fique por dentro do mundo da construção civil.
Cimento Certo
Conheça os 4 tipos de cimento Itambé e a melhor indicação de uso para argamassa e concreto.
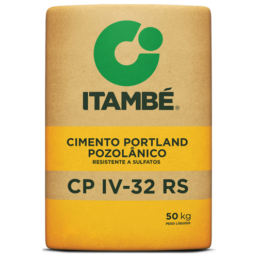
Massa Cinzenta
Cooperação na forma de informação. Toda semana conteúdos novos para você ficar por dentro do mundo da construção civil.
15/05/2024
MASP realiza o maior projeto de restauro desde a sua inauguração
MASP passa por obras de restauro em suas estruturas. Crédito: Assessoria de Imprensa / MASP Quem passa pela Avenida Paulista vem notando uma diferença significativa na…
25/06/2025
Obras no Aeroporto de Congonhas avançam
Em abril de 2025, o Aeroporto de Congonhas completou 89 anos. Em abril de 2024, o aeroporto anunciou uma reestruturação e desde então vem avançando com as obras e reformas. Com…
25/06/2025
Santa Catarina atrai investidores com projetos inovadores que transformam o litoral em vitrine mundial
Santa Catarina está consolidando sua posição como referência nacional em inovação no setor imobiliário, turístico e de lazer. Em breve, na região, serão inaugurados…
25/06/2025
Relacionamento pós-entrega: o novo valor das construtoras no mercado imobiliário para fidelizar clientes
A entrega das chaves de um imóvel não marca o fim do trabalho de uma construtora. Pelo menos não para empresas que apostam na construção de vínculos sólidos com seus clientes. O…
Cimento Certo
Conheça os 4 tipos de cimento Itambé e a melhor indicação de uso para argamassa e concreto.
Use nosso aplicativo para comparar e escolher o cimento certo para sua obra ou produto.
Cimento Portland pozolânico resistente a sulfatos – CP IV-32 RS
Baixo calor de hidratação, bastante utilizado com agregados reativos e tem ótima resistência a meios agressivos.
Cimento Portland composto com fíler – CP II-F-32
Com diversas possibilidades de aplicações, o Cimento Portland composto com fíler é um dos mais utilizados no Brasil.
Cimento Portland composto com fíler – CP II-F-40
Desempenho superior em diversas aplicações, com adição de fíler calcário. Disponível somente a granel.
Cimento Portland de alta resistência inicial – CP V-ARI
O Cimento Portland de alta resistência inicial tem alto grau de finura e menor teor de fíler em sua composição.
Cimento Certo
Conheça os 4 tipos de cimento Itambé e a melhor indicação de uso para argamassa e concreto.
Use nosso aplicativo para comparar e escolher o cimento certo para sua obra ou produto.
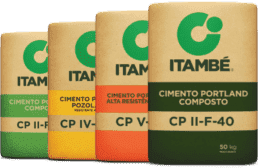